A parada não programada é um dos maiores desafios enfrentados pela indústria moderna. Quando um equipamento falha inesperadamente, toda a cadeia produtiva pode ser comprometida, resultando em atrasos na produção, custos elevados e perda de competitividade.
Mas quais são as principais causas desse problema? E quais setores sofrem mais com esse impacto? A seguir, exploramos os principais dados sobre paradas não programadas e como elas afetam diretamente a produtividade industrial.
O impacto financeiro das paradas não programadas
Os impactos financeiros desse problema são alarmantes. Segundo um levantamento da Siemens, empresas da Fortune Global 500 perdem, em média, 11% de seu faturamento anual devido a paradas não programadas, o que equivale a aproximadamente US$ 1,5 trilhão em perdas todos os anos.
Além disso, os custos dessas interrupções cresceram 65% nos últimos dois anos, impulsionados pelo aumento dos preços dos insumos, escassez de componentes e falta de profissionais especializados.
O custo médio de uma única hora de parada pode variar de US$ 39 mil em indústrias de bens de consumo até US$ 2 milhões na indústria automotiva.
Custo médio anual por planta industrial
Já o custo médio anual por planta industrial também cresceu exponencialmente, chegando a US$ 129 milhões por fábrica. Esse aumento se deve a uma série de fatores, como inflação, dificuldades na cadeia de suprimentos e escassez de mão de obra especializada, que dificultam o reparo rápido dos equipamentos.
Além disso, muitas empresas ainda operam com modelos de manutenção corretiva, ou seja, aguardam a falha para agir, o que agrava os prejuízos e prolonga o tempo de inatividade.
Os setores mais afetados pelas paradas não programadas
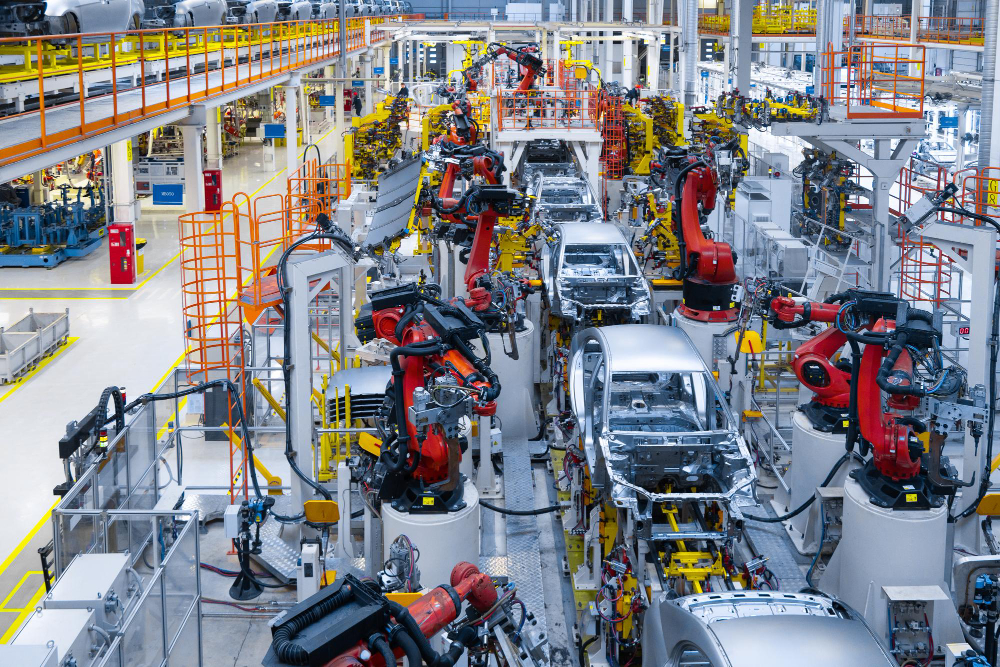
Embora todas as indústrias enfrentem desafios relacionados ao downtime, alguns setores são mais impactados do que outros. O custo por hora de parada pode variar drasticamente, dependendo da complexidade dos processos produtivos e do nível de automação.
Indústria Automotiva
- Custo por hora de parada: acima de US$ 2 milhões
- Com processos altamente integrados e produção em larga escala, qualquer interrupção pode gerar enormes gargalos logísticos e atrasos na entrega de veículos.
Setor de Óleo & Gás
- Custo por hora de parada: US$ 500 mil
- O alto custo operacional e a criticidade das operações tornam esse um dos setores mais impactados, com paradas resultando em grandes perdas de produção e riscos ambientais.
Bens de Consumo Rápido (FMCG)
- Custo por hora de parada: US$ 39 mil
- Apesar de ter um impacto financeiro menor que outros setores, a paralisação de máquinas de produção em série pode afetar o abastecimento do mercado e comprometer cronogramas de distribuição.
Indústria Pesada
- Custo médio anual por planta: US$ 128 milhões
- Setores como mineração e siderurgia dependem de equipamentos de grande porte, onde qualquer falha mecânica pode exigir longos períodos de manutenção, impactando diretamente a produtividade.
A frequência e duração das paradas na indústria
Além do custo elevado, as paradas não programadas são frequentes e prolongadas. O estudo aponta que, em média, as fábricas registram 20 incidentes de parada por mês, resultando em 25 horas de inatividade durante o mesmo período.
Embora o número total de ocorrências tenha diminuído nos últimos anos, o tempo perdido permanece alto, o que sugere que as falhas estão se tornando mais complexas e demoradas para serem resolvidas.
Isso reforça a importância de estratégias proativas de manutenção e identificação eficiente de componentes críticos, garantindo que problemas sejam resolvidos antes mesmo de se tornarem uma ameaça à operação.
Por que os custos das paradas não programadas aumentaram tanto?
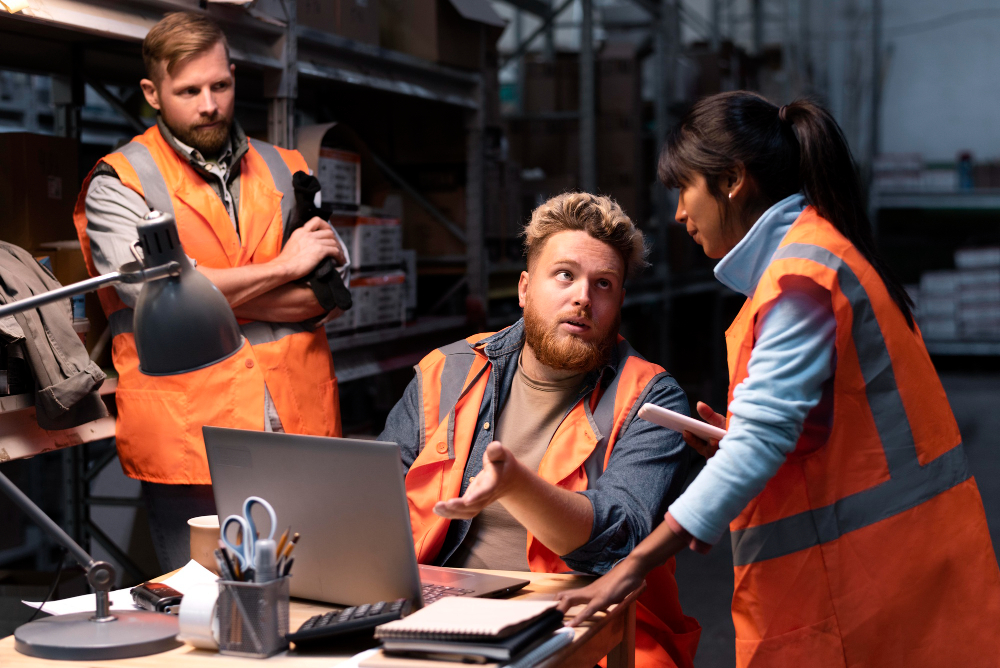
Os custos das paradas industriais cresceram exponencialmente nos últimos anos. Três fatores principais impulsionaram esse aumento:
1. Inflação e aumento dos preços de insumos
O encarecimento de peças e materiais fez com que o custo da manutenção corretiva se tornasse mais elevado.
2. Problemas na cadeia de suprimentos
Com a escassez de componentes eletrônicos e mecânicos, muitas empresas enfrentam dificuldades para encontrar peças sobressalentes no prazo adequado, prolongando os tempos de reparo.
3. Falta de mão de obra qualificada
O setor industrial vem sofrendo com a escassez de engenheiros e técnicos experientes, dificultando a realização de manutenções ágeis e eficientes.
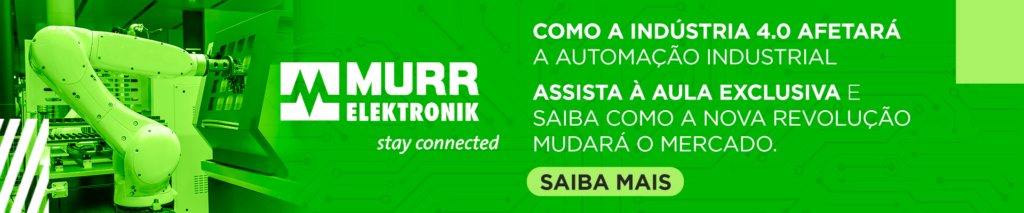
Como reduzir as paradas não programadas na indústria?
Com o avanço das tecnologias, diversas soluções surgiram para minimizar o impacto das paradas inesperadas. Empresas que adotaram estratégias preditivas e automação conseguiram reduzir em até 50% a incidência de falhas inesperadas.
Implementação de manutenção preditiva
O uso de sensores e softwares de análise permite prever falhas antes que elas aconteçam, reduzindo o tempo de inatividade.
Monitoramento de condição em tempo real
Sistemas IoT ajudam a acompanhar o desempenho dos equipamentos, identificando anomalias antes que se tornem falhas críticas.
Previsão de vida útil de componentes
Soluções modernas permitem calcular a vida útil dos ativos industriais, garantindo substituições preventivas antes que ocorram falhas.
Otimização da identificação industrial
A identificação clara e durável de componentes críticos facilita a rastreabilidade e agiliza manutenções, evitando erros e atrasos nos processos de reparo.
Veja também: Identificação de painéis elétricos conforme NR10
O papel da identificação industrial na redução de paradas não programadas

Além das estratégias preditivas e do monitoramento contínuo de equipamentos, um fator muitas vezes subestimado na redução de paradas não programadas é a identificação eficiente de componentes industriais.
A falha na rastreabilidade de peças e equipamentos pode aumentar significativamente o tempo de inatividade, dificultando a realização de manutenções corretivas e preventivas.
Na prática, a ausência de etiquetas compromete a identificação rápida de componentes essenciais, gerando atrasos desnecessários na substituição de peças e no diagnóstico de falhas.
Etiquetas industriais metálicas
Para que a identificação cumpra seu papel na redução de downtime, as etiquetas utilizadas devem ser projetadas para suportar as condições severas da indústria. Em muitos segmentos, os equipamentos estão expostos a fatores como altas temperaturas, umidade, produtos químicos, abrasão e raios UV, o que pode comprometer a legibilidade e a durabilidade de etiquetas convencionais.
Entre as opções disponíveis no mercado, as etiquetas metálicas se destacam como a alternativa mais confiável para ambientes industriais exigentes. Elas oferecem vantagens como:
Resistência a temperaturas extremas
Etiquetas metálicas feitas de aço inoxidável ou alumínio anodizado suportam variações térmicas severas, garantindo que as informações permaneçam visíveis mesmo em ambientes de alta ou baixa temperatura.
Durabilidade contra abrasão e corrosão
O contato constante com agentes químicos e superfícies abrasivas pode desgastar rapidamente etiquetas convencionais. Já as metálicas resistem a esse desgaste, mantendo sua integridade ao longo do tempo.
Legibilidade permanente
A gravação em etiquetas metálicas não desbota e nem se apaga com o tempo, garantindo que a identificação permaneça visível mesmo após anos de uso, o que é essencial para o rastreamento eficiente de peças e componentes, especialmente em setores como automação industrial, mineração, petróleo e gás, e indústria pesada.
Impressora MP-LM 1M: uma solução definitiva para identificação industrial
Para garantir a identificação eficiente e durável de componentes industriais, é fundamental contar com soluções tecnológicas avançadas.
Nesse contexto, a MP-LM 1M da Murrelektronik se destaca como a escolha ideal para indústrias que buscam qualidade, precisão e resistência em suas etiquetas de identificação.
Por que a MP-LM 1M é a melhor opção para marcação industrial?
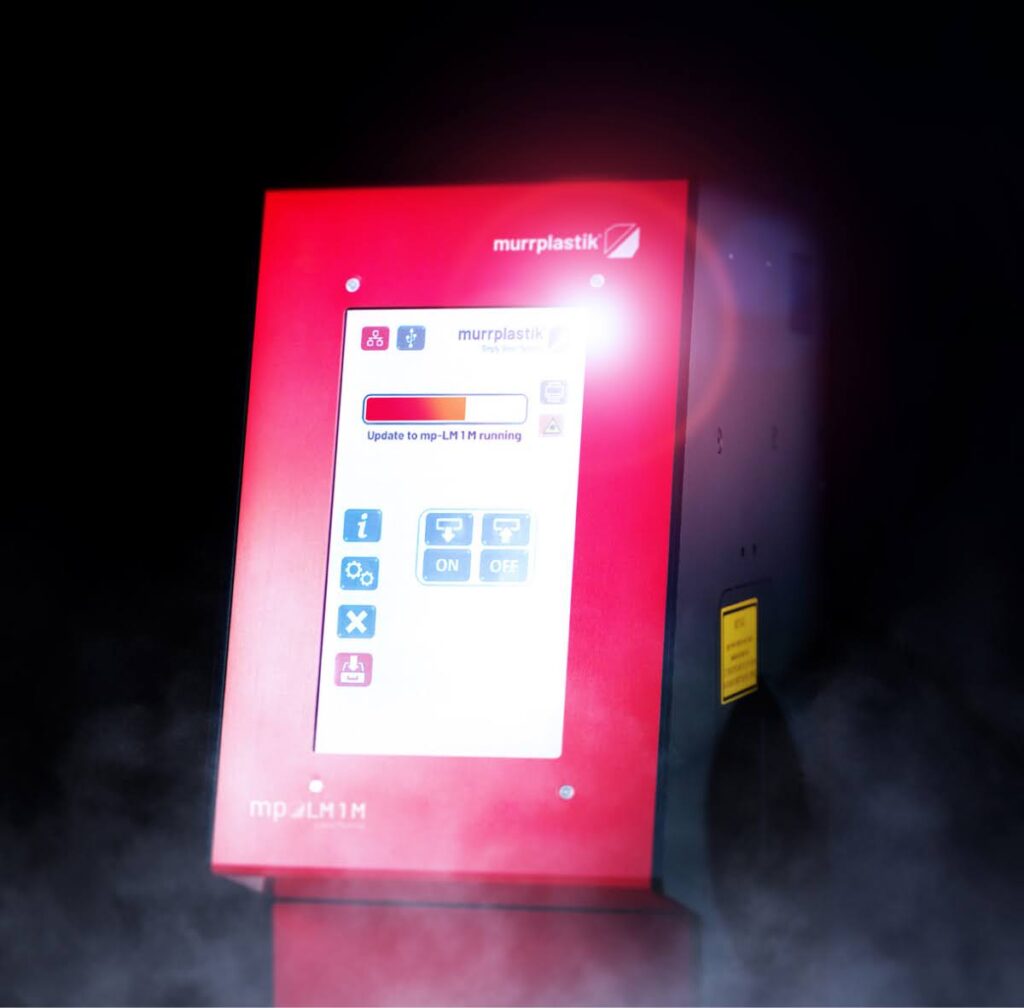
- Gravação a laser de alta precisão – Garante marcações permanentes e de fácil leitura.
- Eliminação de consumíveis – Sem necessidade de tintas ou adesivos, reduzindo custos operacionais.
- Resistência a ambientes agressivos – A marcação a laser suporta calor, umidade, produtos químicos e abrasão.
- Versatilidade – Perfeita para identificação de cabos, painéis elétricos, máquinas e componentes industriais.
- Facilidade de operação – Equipamento compacto e intuitivo, com interface amigável para personalização de etiquetas.
Com a MP-LM 1M, garanta que seus componentes estejam sempre corretamente identificados, reduza erros, agilize a manutenção e minimize as chances de falhas inesperadas.
Saiba mais!
Conheça a MP-LM 1M e como otimizar a identificação industrial, reduzir falhas e evitar paradas inesperadas. Clique no banner e conheça a solução!
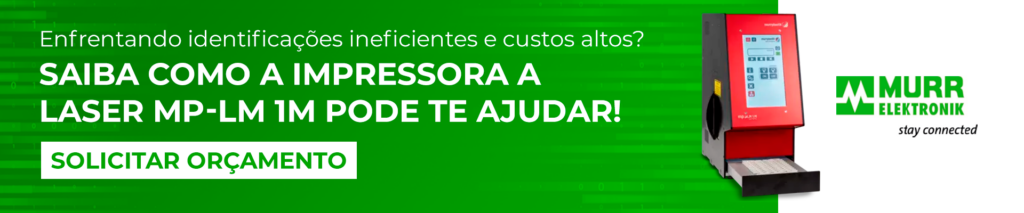